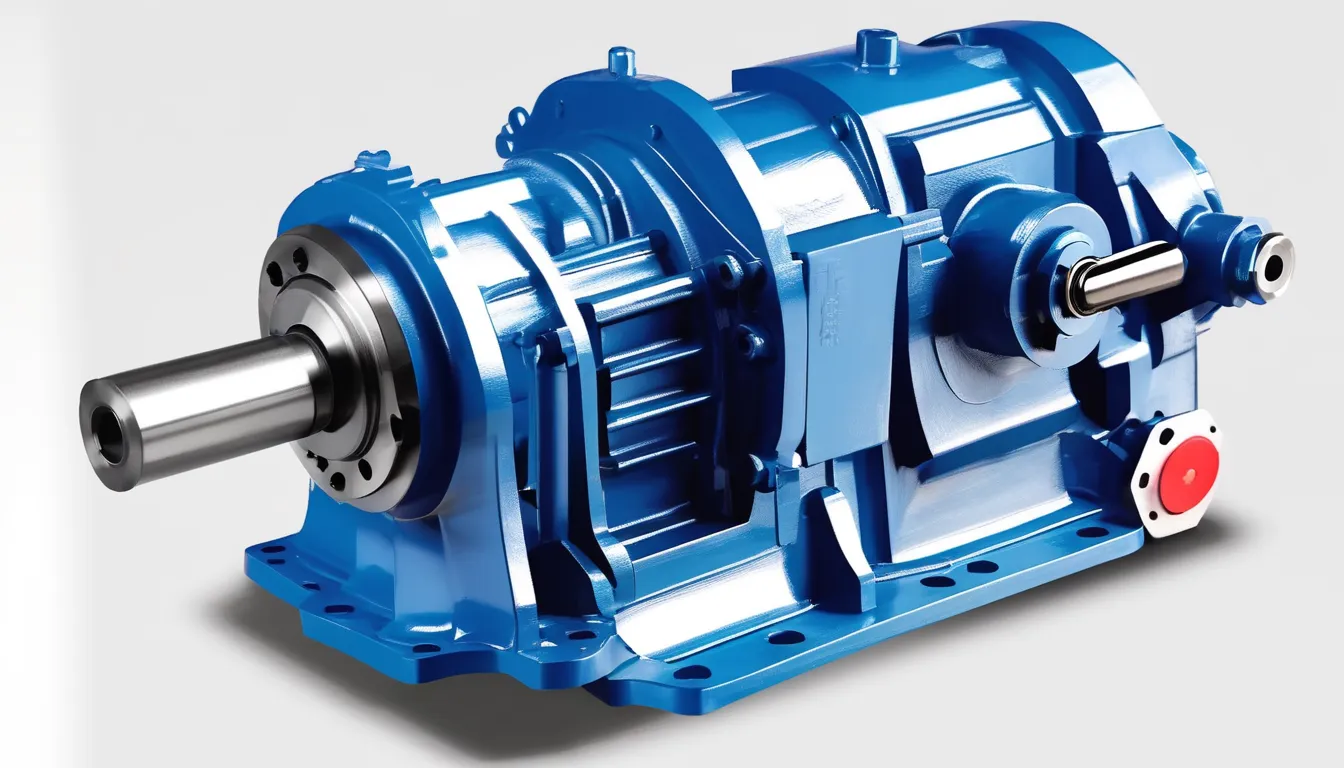
When you consider the intricacies of gearbox design, it’s clear that every choice impacts energy efficiency. You might not realize it, but elements like material selection and gear configuration can significantly influence performance and costs. For example, opting for helical gears over spur gears could yield better results in smoothness and friction reduction. But what about the latest innovations in gearbox engineering? Understanding these developments could transform your approach to machinery and energy consumption, leading to more sustainable practices. The next steps could reveal even more surprising connections.
Importance of Gearbox Design
When it comes to machinery, the importance of gearbox design can’t be overstated. A well-designed gearbox directly influences the efficiency and performance of the entire system. You’ll find that the right design minimizes energy losses, ensuring that more power is transmitted effectively from the motor to the driven equipment. This efficiency not only saves energy costs but also extends the lifespan of the components involved.
Choosing the appropriate materials and manufacturing techniques is crucial. If you overlook these factors, you risk dealing with premature wear, increased maintenance, and potential system failures. A robust design also accounts for the specific application and operational conditions, such as load requirements and speed variations.
Moreover, the layout of gears impacts noise levels and vibration. A high-quality gearbox can significantly reduce these issues, leading to smoother operation and improved user experience.
When you prioritize gearbox design, you’re investing in a reliable foundation for your machinery. In the long run, this attention to detail helps you achieve better overall performance and energy efficiency, reinforcing the significance of thoughtful gearbox design in any engineering project.
Types of Gearbox Configurations
A well-thought-out gearbox design often leads to exploring various gearbox configurations, each tailored for specific applications and performance needs.
You’ll come across several types, starting with the simple spur gearbox. This configuration features straight-cut teeth, making it efficient for transmitting power in a straight line, though it may generate noise at high speeds.
Next, consider helical gearboxes, which have angled teeth that provide smoother operation and quieter performance. They’re great for applications requiring higher torque and load capacity.
If you need to change the direction of rotation, bevel gearboxes come into play. They allow for power transmission at right angles and are often used in applications like automotive differentials.
Planetary gearboxes offer a compact design with high torque capacity, making them popular in robotics and aerospace. They consist of a central sun gear, planet gears, and a ring gear, providing versatility and efficiency.
Lastly, worm gearboxes are known for their ability to achieve high gear reductions in a compact space, but they can be less efficient due to friction.
Each configuration has its strengths, so understanding them helps you choose the right gearbox for your needs.
Factors Affecting Energy Efficiency
Energy efficiency in gearbox design hinges on several critical factors that can significantly impact performance. Understanding these factors can help you make better decisions in your designs and applications.
First, the choice of materials plays a vital role. Lightweight, high-strength materials can reduce energy loss due to inertia. Next, the precision of manufacturing affects how well the gears mesh together. Poorly manufactured gears lead to increased friction, which can cause energy losses. Lubrication is another key factor; using the right lubricant minimizes friction and wear, enhancing efficiency.
Finally, gear configuration and design influence energy transfer. For instance, helical gears offer smoother operation compared to spur gears, reducing energy loss.
Here’s a summary of these factors:
Factor | Impact on Efficiency |
---|---|
Material Choice | Reduces inertia and weight |
Manufacturing Precision | Enhances gear meshing |
Lubrication Type | Minimizes friction and wear |
Gear Configuration | Influences energy transfer |
Gear Design | Affects operational smoothness |
Innovations in Gearbox Engineering
Recent advancements in gearbox engineering have transformed how we approach design and efficiency.
You’ll find that these innovations not only enhance performance but also optimize energy consumption, making your systems more sustainable.
Here are three key innovations that are shaping the industry:
- Smart Gearbox Monitoring: With IoT technology, you can now monitor gearbox performance in real-time. This allows for predictive maintenance, reducing downtime and increasing efficiency.
- Advanced Materials: The use of lightweight, high-strength materials helps in reducing friction and weight within the gearbox. This means less energy is wasted, and your systems can operate more efficiently.
- Modular Designs: Innovative modular gearbox designs allow for easier upgrades and customization. You can adapt your system to specific needs without starting from scratch, ensuring optimal performance and energy use.
These breakthroughs in gearbox engineering not only enhance performance but also play a critical role in achieving energy efficiency.
Case Studies and Applications
Over the past few years, various industries have successfully implemented innovative gearbox designs to enhance both performance and energy efficiency.
For instance, in the automotive sector, manufacturers have adopted dual-clutch transmissions that optimize gear shifts, reducing energy loss during acceleration. You’ll find that this technology not only improves fuel efficiency but also enhances overall driving experience.
In the renewable energy field, wind turbine manufacturers have developed gearboxes specifically designed to withstand high torque and variable conditions. These customized designs significantly increase energy conversion rates, making wind power more viable.
When you look at industrial applications, companies have shifted to helical gear designs that minimize friction and heat generation, leading to lower operational costs and longer equipment life.
Additionally, in the robotics industry, precision gearboxes are used to enhance the energy efficiency of robotic arms and automated systems. By utilizing lightweight materials and advanced gearing configurations, these systems consume less power while maximizing output.
Each of these case studies illustrates how strategic industrial gearbox manufacturer design choices can lead to substantial energy savings, proving that efficient design is crucial in today’s competitive landscape.
Conclusion
In summary, understanding the connection between gearbox design and energy efficiency is essential for optimizing performance and reducing operational costs. By choosing the right configuration and paying attention to factors like material and lubrication, you can significantly enhance efficiency. Innovations in gearbox engineering continue to push boundaries, making it crucial to stay updated on the latest advancements. Ultimately, investing in a well-designed gearbox not only boosts energy efficiency but also contributes to the longevity and reliability of your equipment.